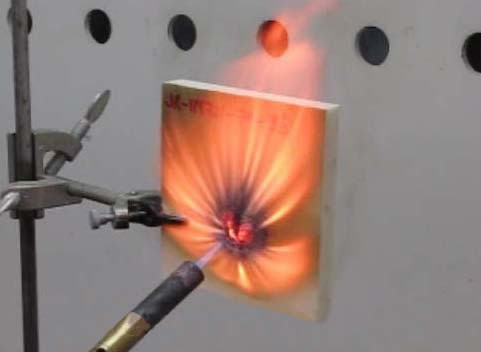
-
5000-2.5 TRX Pouring Foam
5000-2.5 TRX pouring foam is a water-blown foam designed especially for pour casting into molds to create very intricate very diverse parts. This pouring foam is blended to specifically designed re-activity molding times such as creme time, gel time, tack-free and overall cure time. The foam contains a bio-based polyol. This pour casting foam may be used in a variety of applications in very diverse industries such as architectural wall and decorative part moldings, furniture and toy markets, specialty part moldings etc.
Please contact our Customer Service and Technical Support Group for any questions or to provide direction with specific selection of a material system, questionable target applications, operational procedures, material pumping/pour machines, safety protection gear and clean-up.
-
Cushion Foam
Cushion Foam is a superior bio-based flexible microcellular open-cell foam designed to deliver very high toughness and durability for diverse fields of application such as furniture seating cushions, automotive seating, house-wraps, play toys, shock and vibration absorption, impact sports padding, sound-proofing, etc. Seating densities normally range from 3-5 pcf. Density formulations may be adjusted to accommodate other very specific requirements including colors.
This unique bio-based high resilient (HR) flexible foam exhibits very low compression set while providing dimensional stability through its wide operating temperature range. Cushion Foam is formulated from special MDI pre-polymers to create very fast production and de-molding cycles.
Please call or email our Technical Support Group for any questions regarding material, application or prospective uses.
-
FireSkin™ Foam
FireSkin Foam is an insulating material designed to withstand direct flame contact. It produces very low smoke and flame spread. The material develops an intumescent fire barrier which provides a protective shield against constant flame and extreme heat conduction to interior surfaces. These closed cell foams range in varing densities from 0.5-50 pcf for use in diverse fire protection system applications. FireSkin Foam is formulated as a Halogen-free, Class 1 fire rated foam containing renewable resource “Green” materials.
FireSkin Foam delivers toughness and dimensional stability from -20F (-29C) to 250 F (130C). It is used in a variety of construction applications such as in roof, wall and floor building insulation and structural sandwich panel construction foam core materials. These materials have been designed to accommodate HFC 245 or Pentane blowing agent for maximum R-values. This material has been designed for use in economical Continous Panel Laminator machines as shown below. See LAB FIRE VIDEO1 here. See LAB FIRE VIDEO2 here.
-
FireSkin™ Foam 0.5
Fireskin Foam 0.5 is a two component, 1-1 parts by volume, light density, spray applied polyurethane foam. To produce Fireskin Foam 0.5 requires the use of an A-Component (ISO) and a B-Component (RESIN), which contains zero ozone depleting blowing agents, catalyst, polyols and flame-retardant materials such as fiberglass, cellulose or other loose fill products. Typical areas where spray polyurethane foam is applied are interior walls, attics, ceilings and spa insulations.
-
I-Skin Foam
I-Skin Foam (Integral-Skin) is a high performance self-skinning foam designed for toughness and durability. Its hardness ranges from semi-rigid to sponge-soft to provide for multi-versatile applications such as commercial impact floor mats, seating cushions, vibration insulators, rigid impact panels, sports equipment, soft/rigid play toys, etc. It may be formulated in any color and many densities to accommodate very specific requirements.
This unique foam exhibits very low compression set while providing dimensional stability through its wide operating temperature range. I-Skin Foam is formulated from special MDI prepolymers to create very fast molding cycles. It is available using water or gas blown formulations. I-skin can also be formulated to meet CAL 117, MVSS 302 and FAR 25.853a
Please call or email our Technical Support Group for any questions regarding material, application or prospective uses.
-
Pole-Setting Rigid Foam
Pole Setting Foam is designed specifically for fast-setting structural pole-setting applications such as utility/telephone poles, flag poles, fence posts, etc. It is a tough 100% solids non-hydrophilic 6 pcf foam formulation exhibiting 100 psi compressive strength to provide secure fast-installations. The foam may be used directly in holes which contain a water volume of less than 5% of the total hole volume. It delivers excellent chemical resistance and may be applied in dirt having a wide pH range. For special applications a 9.0 PCF density is also available with the same characteristics, but higher compression strength.
Pole-Setting Foam is mixed 1:1 using a hand-held drill jiffy mixer until both components mix into a uniform color (approx 1min). It is then poured directly around the pole into the surrounding hole which obtains a firm material set-up within 15 minutes. The foam may be covered with dirt immediately after it becomes rigid to the touch. It will not be damaged by rain after this point. Material reactivity time may be adjusted to accommodate specific demanding application environments if requested. Please contact Customer Service/ Tech Support for application recommendations and procedures.
-
Pouring Foams
Pouring Foams are a family of rigid water-blown foams designed especially for pour casting into molds to create very intricate very diverse parts. These pouring foam formulations may be custom blended to offer unique mechanical, thermal, non-burning, high compressive/shear strength properties along with specifically designed reactivity molding times such as creme time, gel time, tack-free and overall cure time. SuperSkinSystems offers these properties in a wide range of foam densities. Typical density pouring foams ranges from 2-10 pcf. These foams may also be colored and/or include bio-based polyols to be considered “a green product”. These pour casting foams are seen in a variety of applications in very diverse industries such as architectural wall and decorative part moldings, furniture and toy markets, specialty part moldings etc. Densities of 2-3 pcf have been tested to MIL-P21929C.
Please contact our Customer Service and Technical Support Group for any questions or to provide direction with specific selection of a material system, questionable target applications, operational procedures, material pumping/pour machines, safety protection gear and clean-up.
-
Rigid Building Foams
Rigid Building Foams offer a unique blend of properties which yield excellent mechanical and thermally efficient structures. SSFR foams deliver high compressive/shear strength, insulating capacity, overall toughness and impact resistance. Their high performance strength to weight ratio densities produce a wide range of applications for very diverse industries. As an energy saving material yielding very high insulating values, paralleled with its sound absorbing capability it has seen much use in the architectural and construction industries. Rigid foams are applied in spray or casting formats. Pour casting diversifies its uses to the areas of consumer products manufacturing, mold making, marine docks, flotation, void fill, artwork carving and many industrial and commercial industries. SSFRs may be subsequently color top-coated, textured and clear coated to handle extensive outdoor rugged environments using the ClearSkin system. These materials maintain dimensional stability and will not deform or distort within operating temperature of -100F to 200F. Fire retardant formulations are used in structural public buildings and warehouses. Installation cure times range from 30 sec. to 30 min. depending on application method (spray vs. pour), ambient temperature and humidity. Pour foam applications require longer cure times and caution must be taken for large castings due to inherent exothermic reaction process. SSFRs utilize a standard 2-component liquid pumping machine for both the spray and pour methods of dispensing. Volumetric expansion of SSFR may be formulated up to 140x relative to its original volume depending on required application densities. Densities of 2-3 pcf have been tested to MIL-P21929C.
The Rigid Building Foams are water or gas blown (245 or Pentane) fast-set materials typically used for air-tight insulation applications due to their closed-cellular nature. These foams are premium building products which contribute structural integrity with moisture, air and chemical vapor barrier integrity. High insulating values are attibuted with these foams and as such are commonly in roof, wall and floor insulation applications, commercial freezers and all energy saving applications where high thermal insulating requirements are mandated. Values vary relative to foam densities. Foam coverage per sq.ft. will vary relative to the density also as governed by expansion characteristics, the ambient spray temperature and the substrate temperature.
Please contact our Customer Service and Technical Support Group for any questions or to provide direction with specific selection of a material system, questionalable target surfaces, operational procedures, material pumping/spray machines, spray/pour guns, safety protection gear and clean-up kits.
-
Saddle Foam
Saddle Foam is a unique fast-build 2-component multi-purpose 3.0 pcf structural foam designed specifically for pipeline trench retainment and pipe saddle suspension applications. This tough foam provides excellent uniform cellular foaming to quickly build high strength rigid barriers. The cured foam is hydrophobic, tough and resilient to cracking. It provides excellent bonding to many porous and non-porous substrates such as concrete, metals, fiberglass etc. Specific formulations may be obtained to properly fit demanding applications. Please contact our technical support group for specific substrate application procedures, equipment, safety gear and clean-up kits. Refer to MSDS for material and safety standard procedures.